Liquid CO2, or LCO2, is an excellent solvent for cleaning silicone tubing and elastomers. CO2 is non-toxic, non-flammable, non-corrosive, odorless and chemically stable. The CO2 extraction process uses liquid carbon dioxide to treat silicone elastomers, by removing low molecular volatiles and byproducts such as peroxides after molding or extruding. Liquid CO2 has a very low surface tension and wets the substrate surface very well. The liquid penetrates the whole sponge-like structure of the silicone and dissolves all non-cross-linked compounds. The structure of the vulcanized silicone rubber does not change. This makes the LCO2 process an excellent alternative to the traditional heat curing process or washing process in organic solvents. The process takes place at high pressure between 10-15°C which allows homogenous treatment of the parts.
- Environmentally friendly: no emission of silicone volatiles into the atmosphere
- CO2 is an industrial byproduct and is recycled
- Shorter process time and more silicone volatiles are removed than during traditional heat curing
- High molecular silicone compounds are removed
- EN 14350-2 is fulfilled
- Heat sensitive parts such as 2 component moldings, heat sensitive pigments or active ingredients are not affected
- No ageing effect during treatment, i.e. the mechanical properties remain as molded
- No dust formation (SiO2)
- No post-polymerization (“Slit-healing”).
- Packaging of the treated parts directly after treatment, no cooling step
Case Study: Breast Implants
A common silicone implant used widely around the world are breast implants. Known as a safe alternative used to change the size, shape, and contour of a person’s breast, silicone gel-filled breast implants have become increasingly popular.
Manufacturing of silicone breast implants present cleaning challenges before being approved for human use. Current implant cleaning methods involve solvent washes that are not only time consuming, but hazardous to workers. By using our CO2 extraction process instead, we can remove the contaminants with no added solvents. On top of that we can clean multiple implants in the wash vessel improving on time spent cleaning.
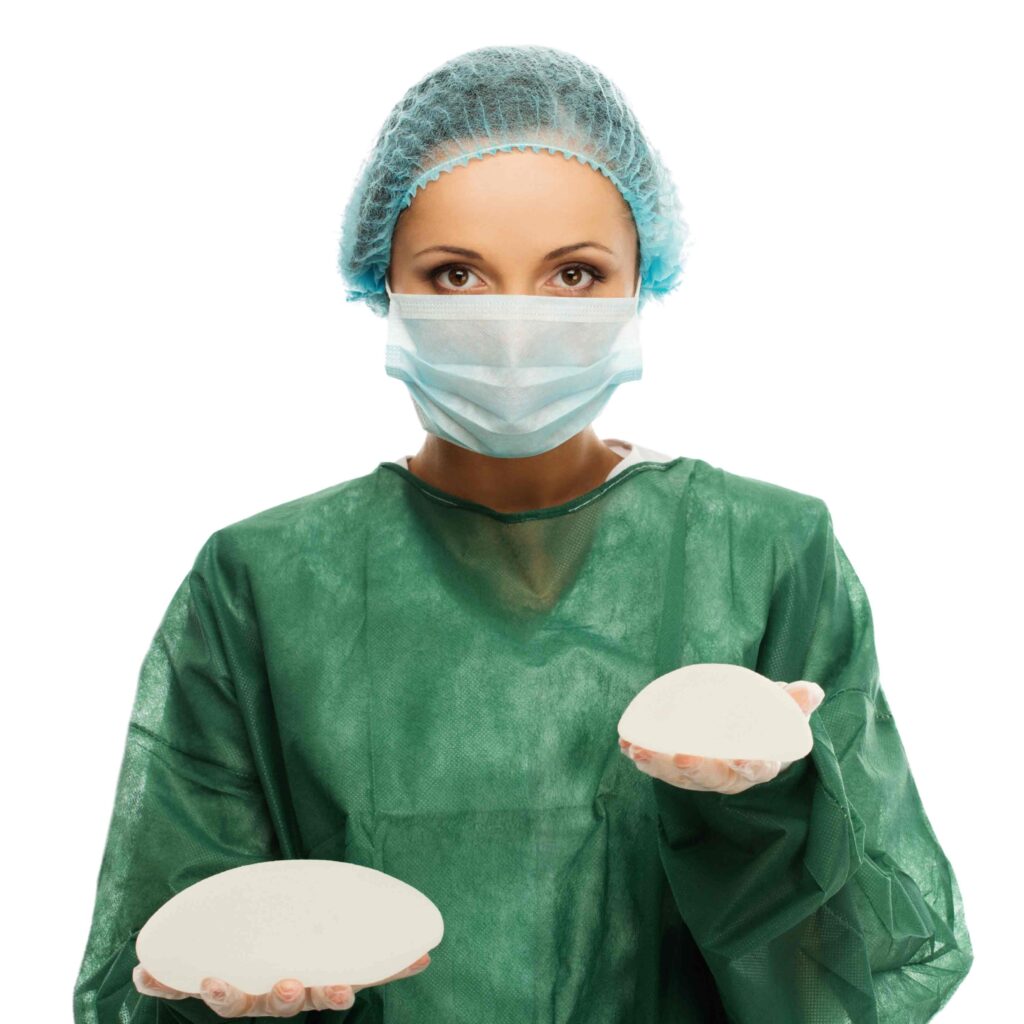
Cool Clean recently worked with a large pharmaceutical industry company to incorporate our unique CO2 technology to help the company solve a health and safety issue for its workers. The company specializes in silicone implants and was having difficulty removing the unreacted monomers from the breast implant material. Their current process involved flammable solvents, which could not be reused in an FDA-controlled process.
Cool Clean Technologies was contacted by the company with the aim to adapt its CO2 technology for a cleanroom environment and apply it to the specific cleaning criteria. After identifying the type of contaminant and particulate, CCT met the clients’ specifications by using a closed-loop liquid CO2 cleaning system. An added benefit was a reduction of cycle time to one-fifth the original time, allowing the company to increase production of implant efficiency.